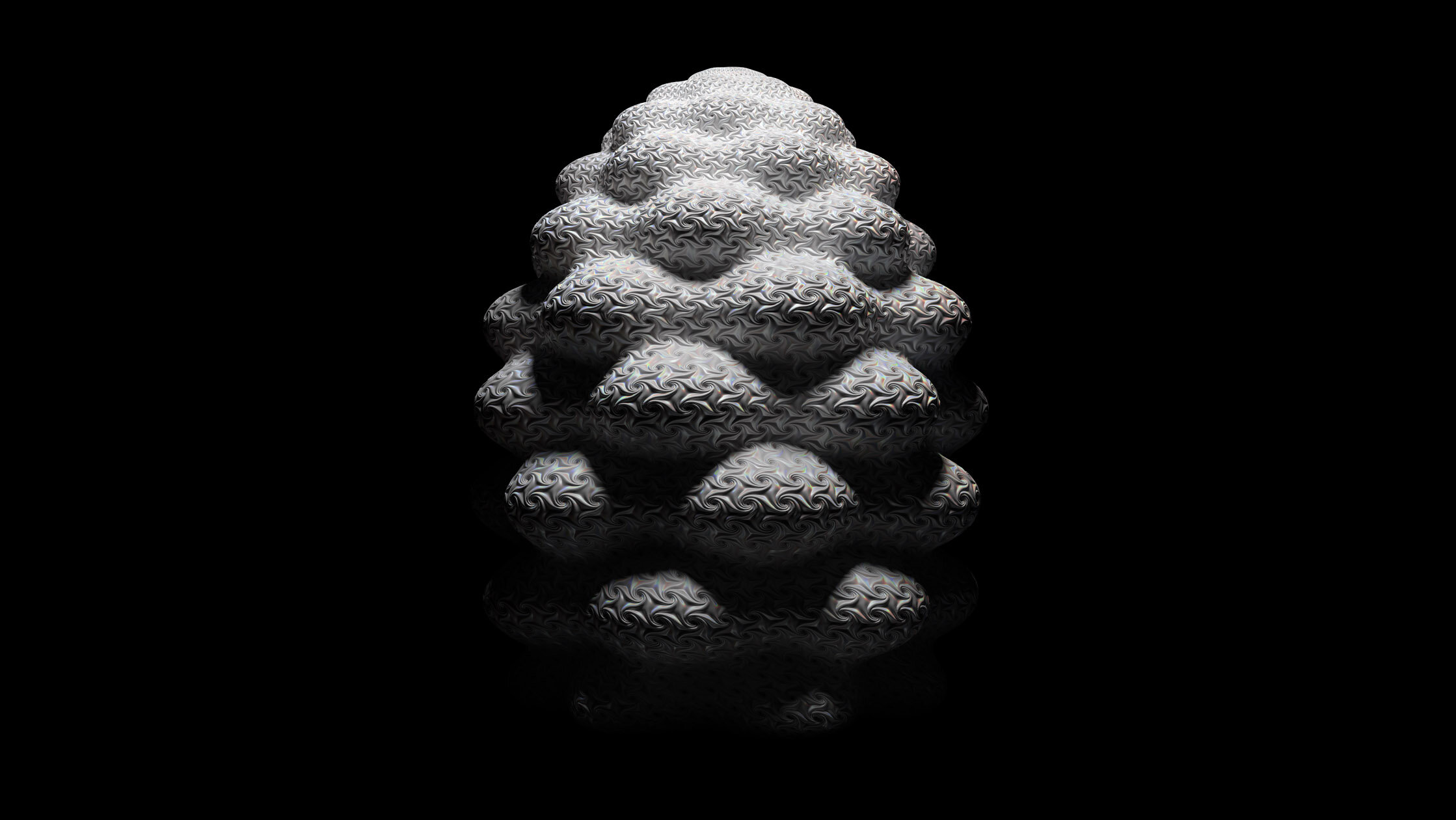
MARS-1 | Strobilus
I had the great pleasure of working with one of my all-time favorite artists, Mario Martinez (aka MARS-1), to create his 11 ft bronze sculpture, “Strobilus.” It was extremely inspiring to work with Mario on such a complex and challenging project that combined the use of new software and fabrication technologies with age-old foundry techniques (executed by the master craftspeople of Artworks Foundry). Mario has long been one of my biggest artistic influences, and it’s been awesome to learn from him as we conquered some intellectual, technical, and aesthetic challenges.
Organic Underlying Form
For his next giant bronze sculpture, Mario envisioned an organic form with bulbs arranged in a pattern not unlike a pine cone (one of his clay explorations of the form is pictured above), with interweaving spirals detailing its surface.
Spiral Lattice
Mario has explored arrays of interacting spirals in a number of his paintings, and he was interested in bringing the concept to the physical world. His vision was to overlay an interlocking spiral pattern onto the larger organic form.
Organic Bulbs
Using Blender 3D, I created a geometric arrangement of metaballs. We experimented with varying parameters of the bulbs to arrive at this final shape. It was important to make sure the topology of the base shape was geometrically flawless in order to precisely position the spiral pattern.
Interlocking Spiral Tessellation
After we modeled the first ideal spiral manually, I figured out a technique to procedurally generate its repetition, seamlessly interconnecting the hexagonal spiral pattern ad infinitum. The procedural setup in Blender is shown below.
Spiral Array Configuration
Synthesis…
Mapping
While I had found an elegant way to create a procedural lattice of interlocking spirals, getting them to map to the organic form proved difficult. In the end, the solution was somewhat brutish, requiring significant processing power and outputting huge files for each bulb. The thing about spirals is that they contain infinite detail in theory, so to crush them into bits at a sufficient resolution to maintain fidelity at an 11 ft. scale meant that the 3D file for each bulb was around 2GB, pushing both the software and hardware to their limits upon each export.
Hand Tuning
After the main pieces were in place, we wanted to tweak the details to perfection. We varied the relative sizes of the spirals to accentuate and interact with the bulbs’ undulating manifold, which also involved finessing the depth of the spirals on each layer. The final challenge was how to treat the top of the sculpture, where the spiral of the bulbs converges to a singularity. I suggested a seven-legged spiral that formed at the confluence of the bulbs. This interacts nicely with the smaller spirals, stretching toward infinity as they round the vortex. The process of iteratively refining the design was aided by the use of of 3D-printed prototypes, which provided valuable insight through a tangible understanding of the sculptural form.
3D Print Prototypes
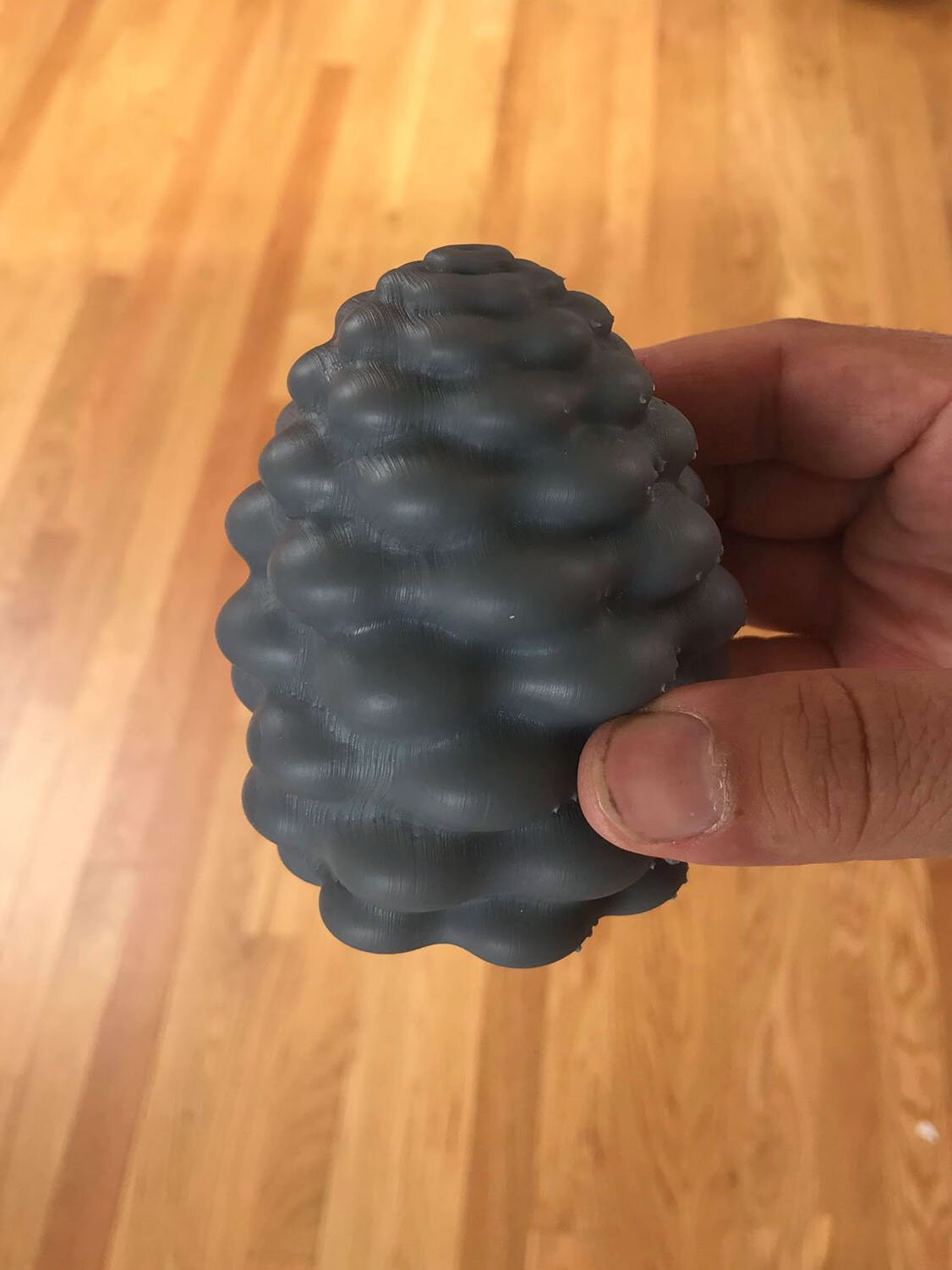
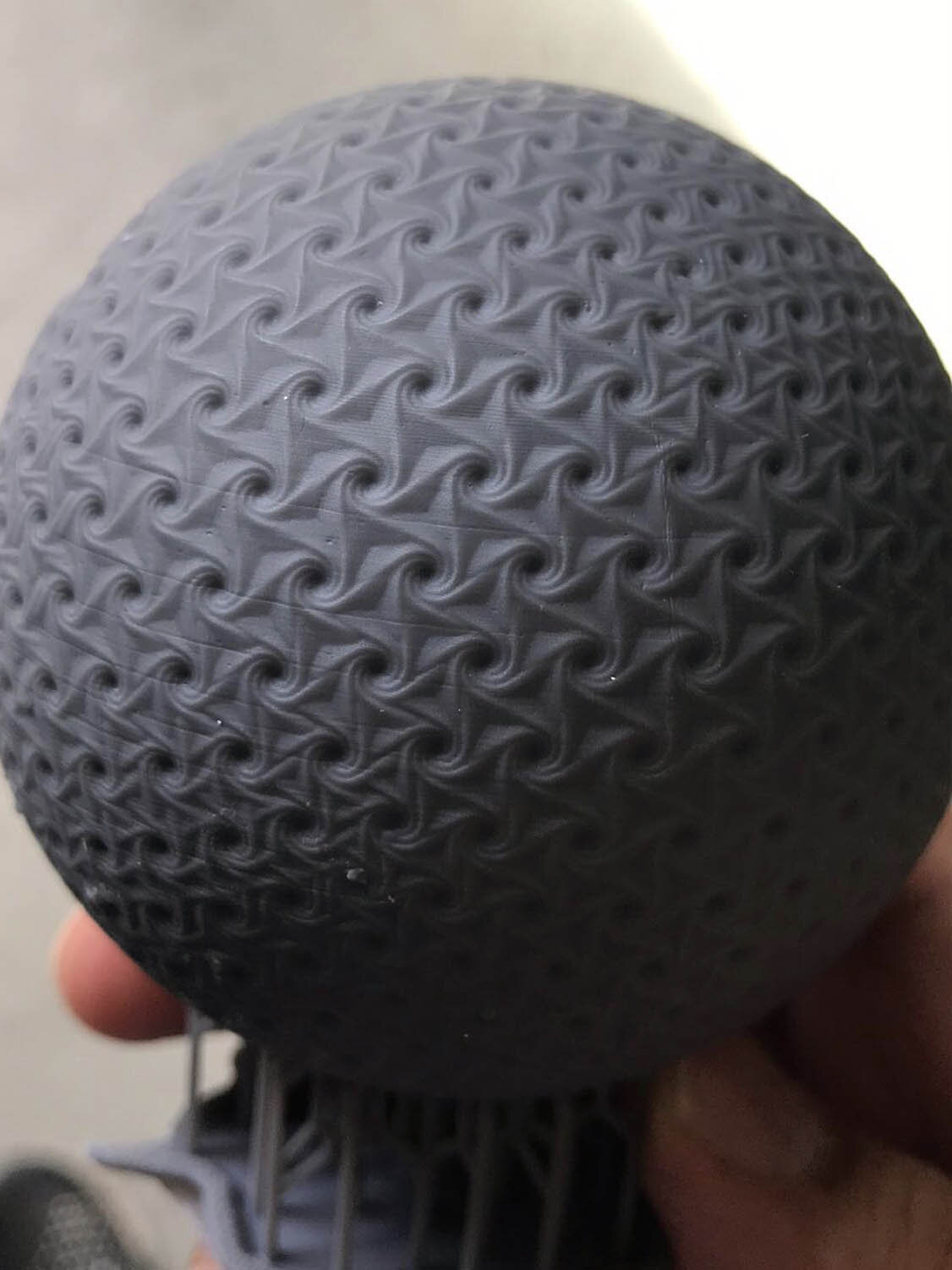
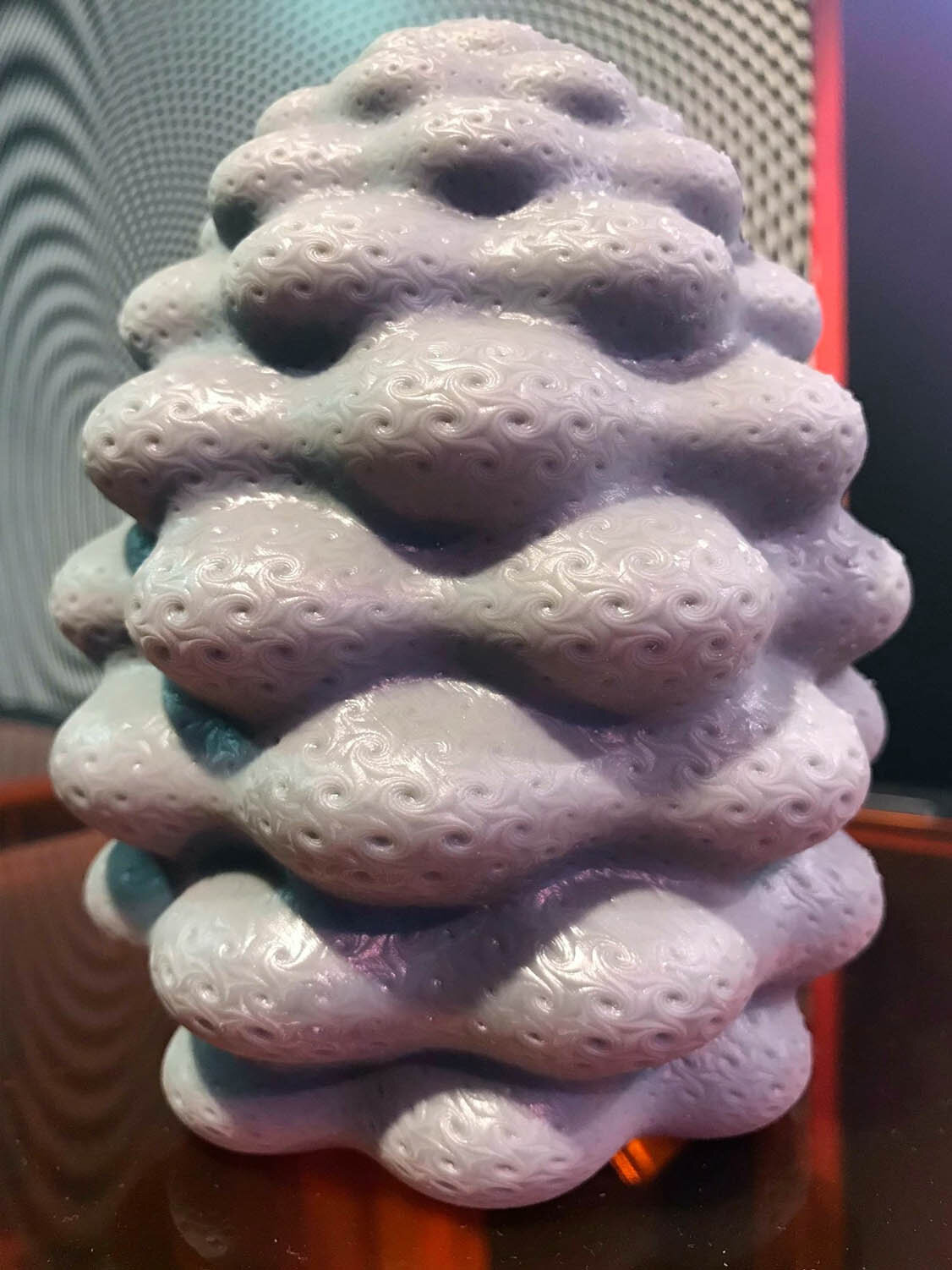
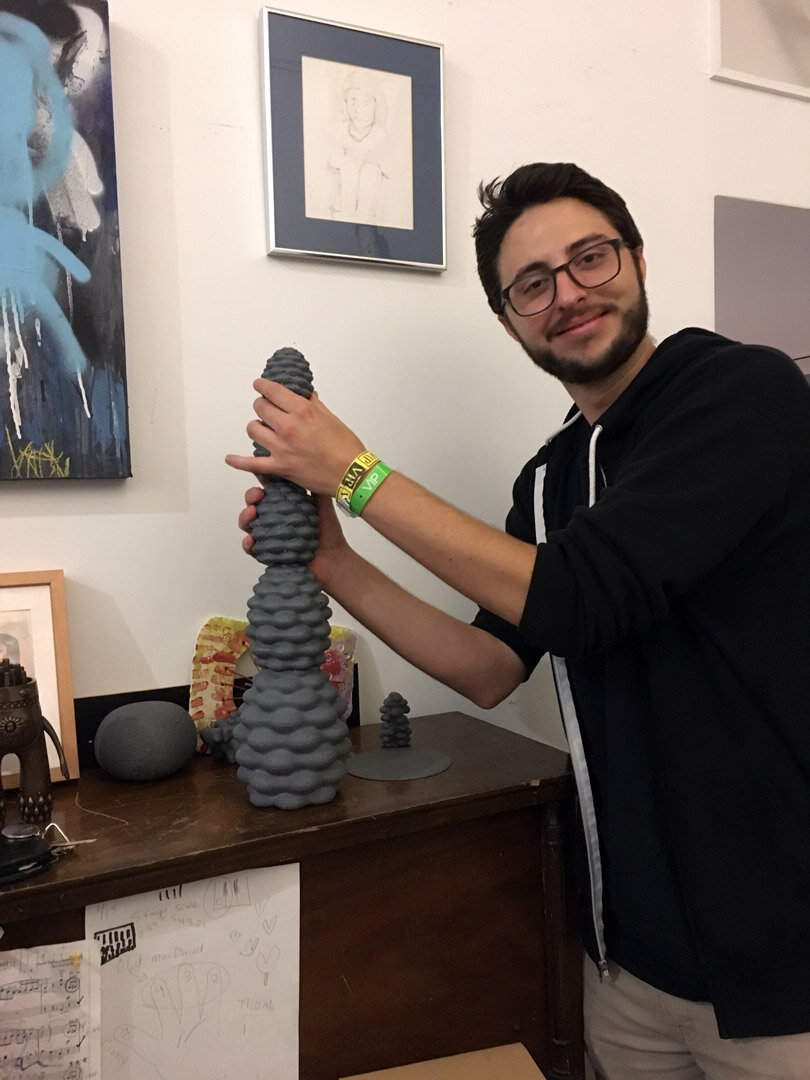
Visualizing at Scale
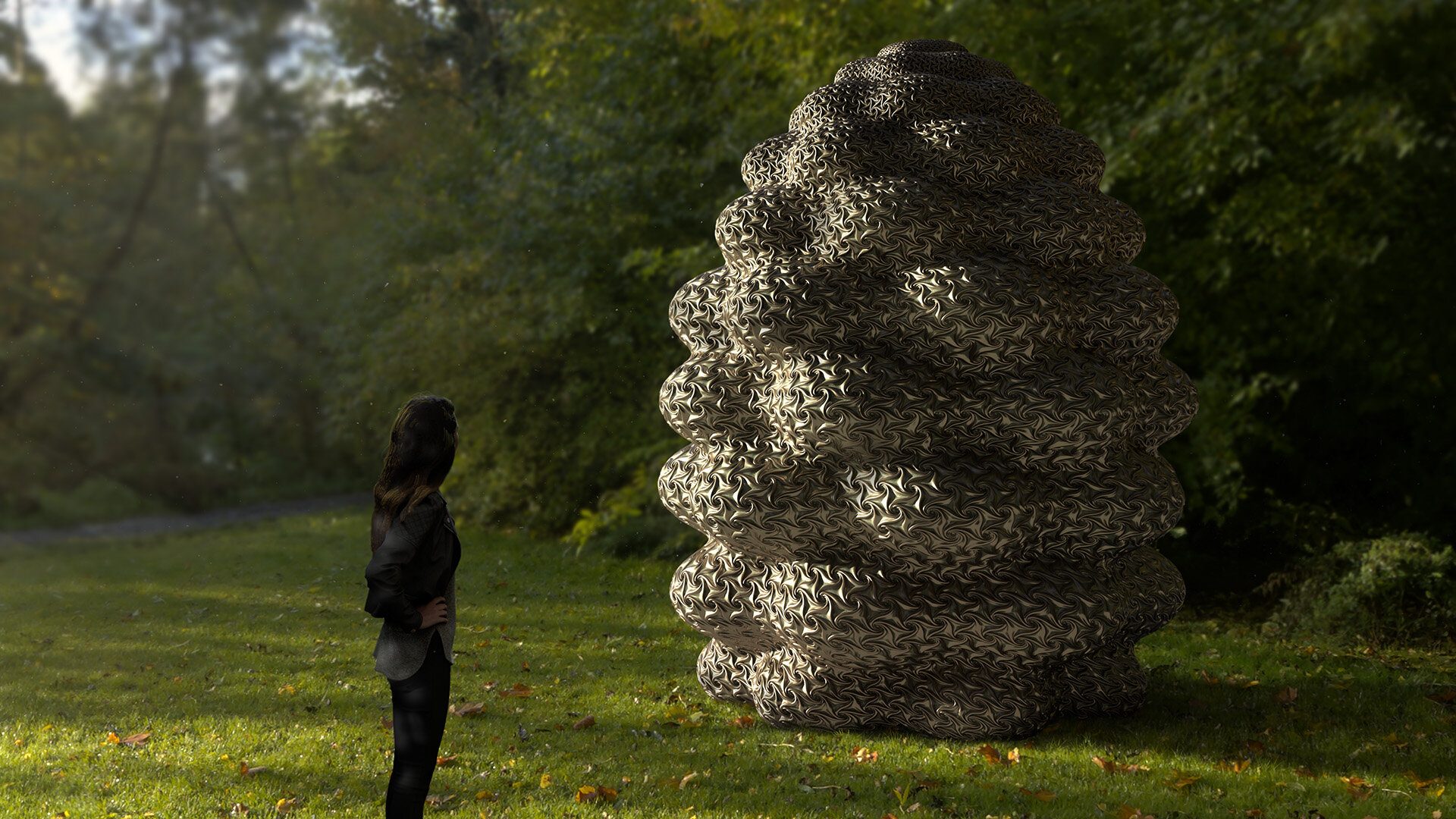
Fabrication Process
It was important to consider the nuances of the fabrication processes, as the sculpture was going to be massive. The production of the sculpture involved technologies both new and old. Large format 3d printing technology enabled the intricate mathematical details of the spiral lattice, and the piecewise bronze casting allowed for the enormous scale. The sculpture is composed of 11 layers of bulbs, and 7 bulbs per layer. In order to maximize efficiency, we designed the bulbs to be rotationally symmetric— a single bulb from each vertical layer (except the top two layers, done as one piece) would be 3D-printed and used to create a mold. Each mold would be used to cast 7 pieces, and at the end all the bulbs would be joined.
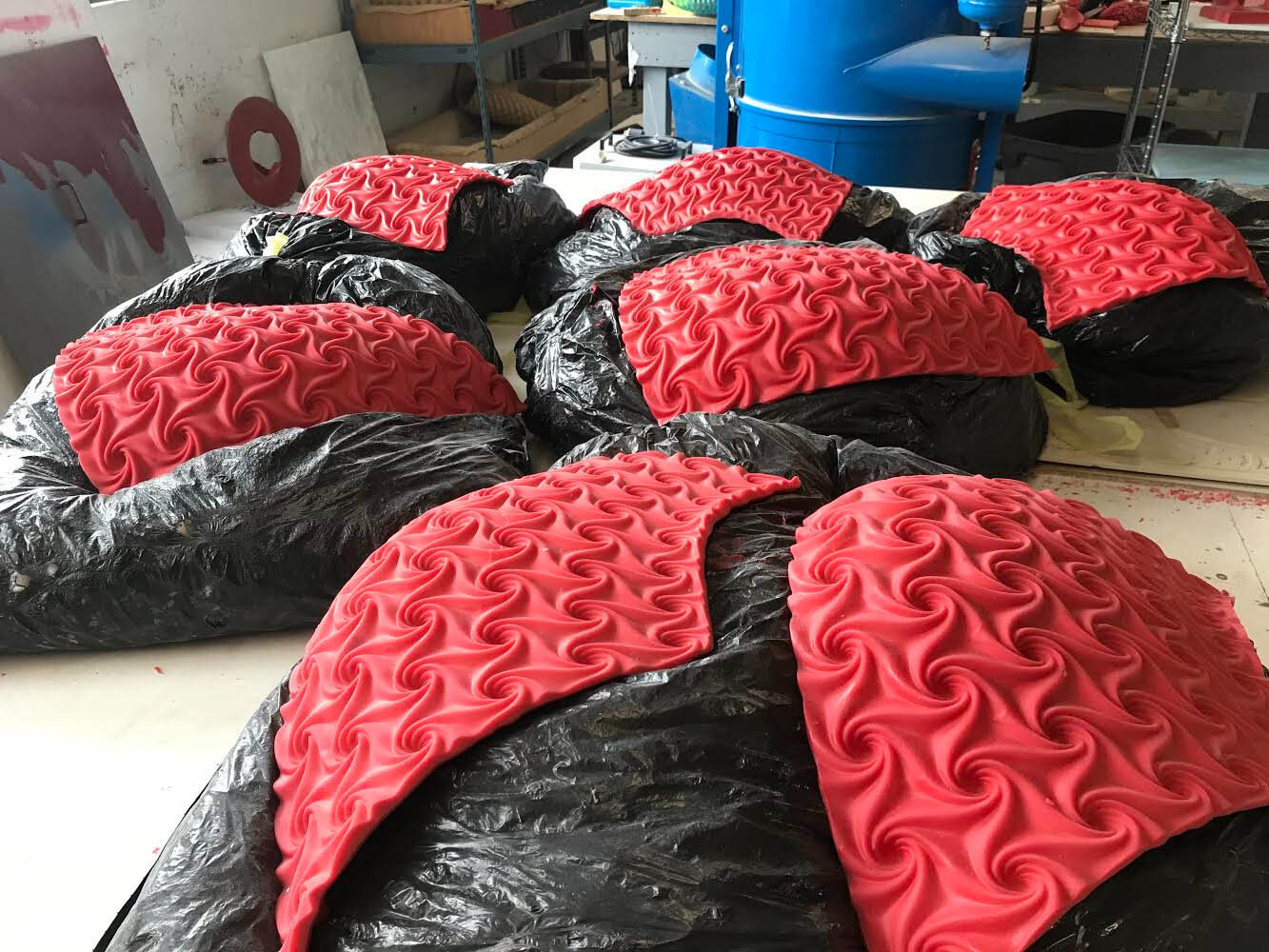
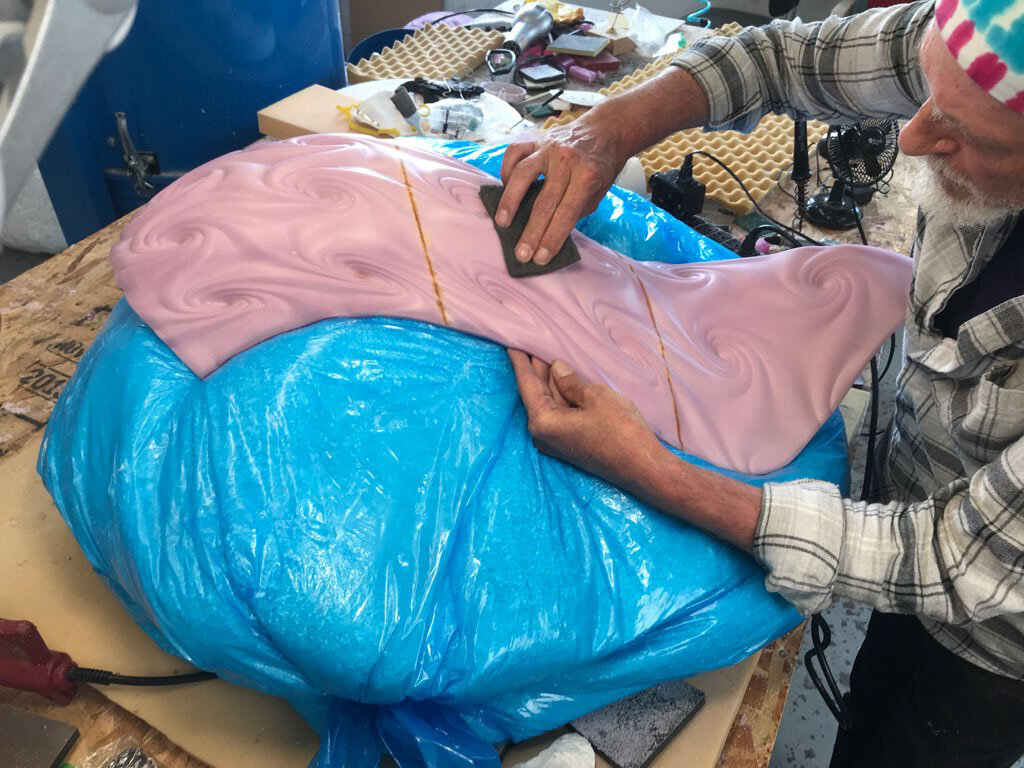
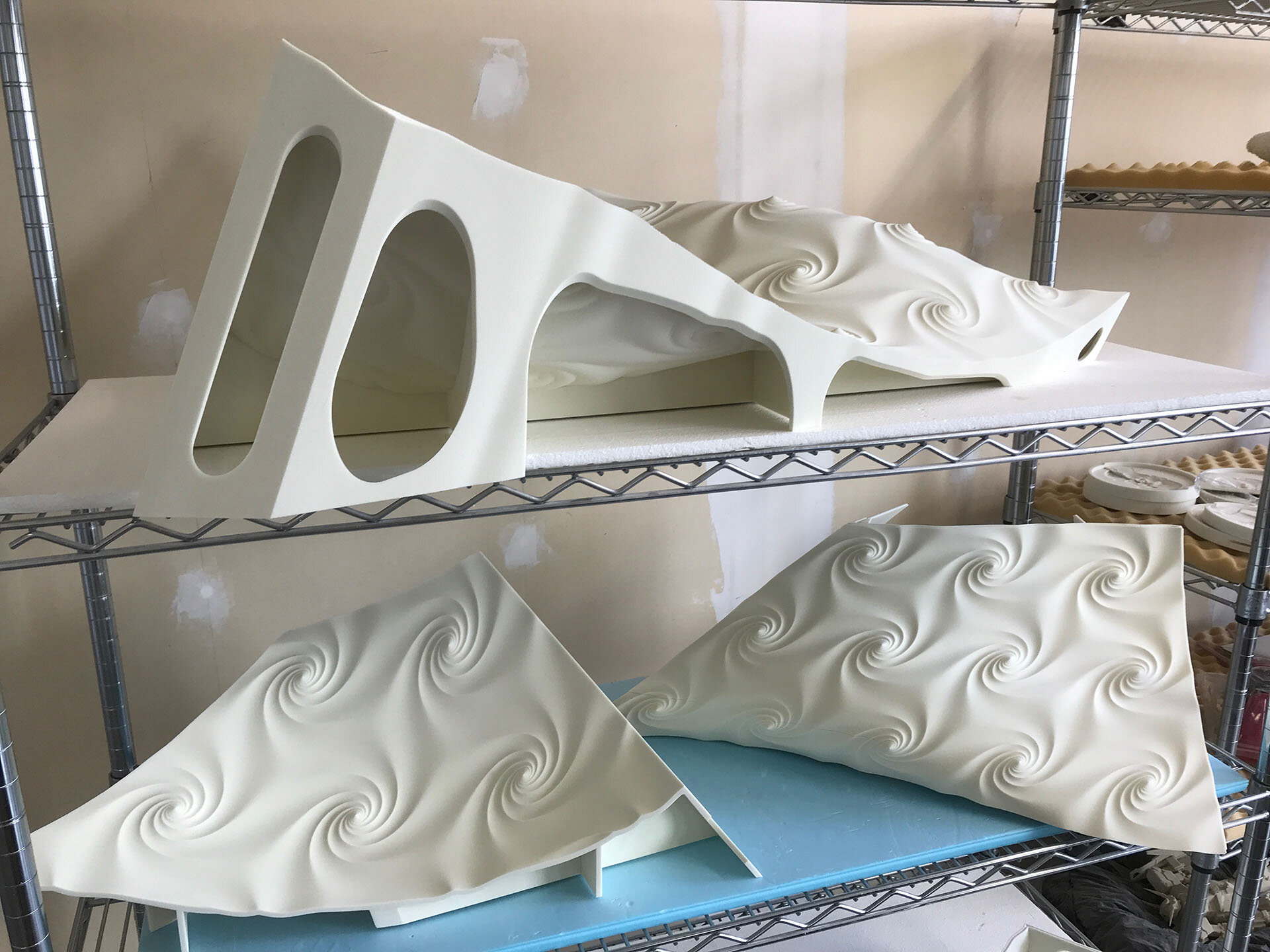
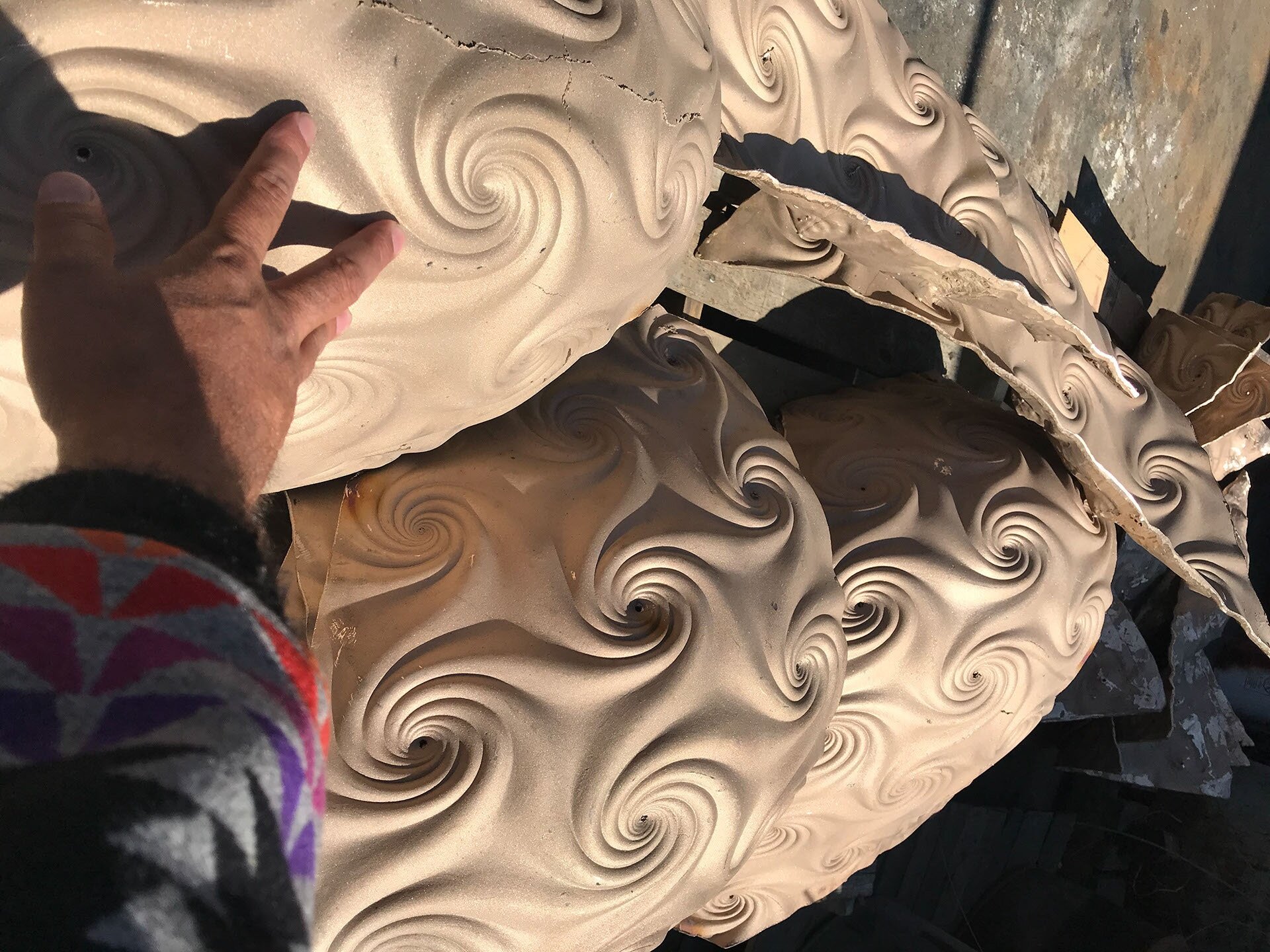

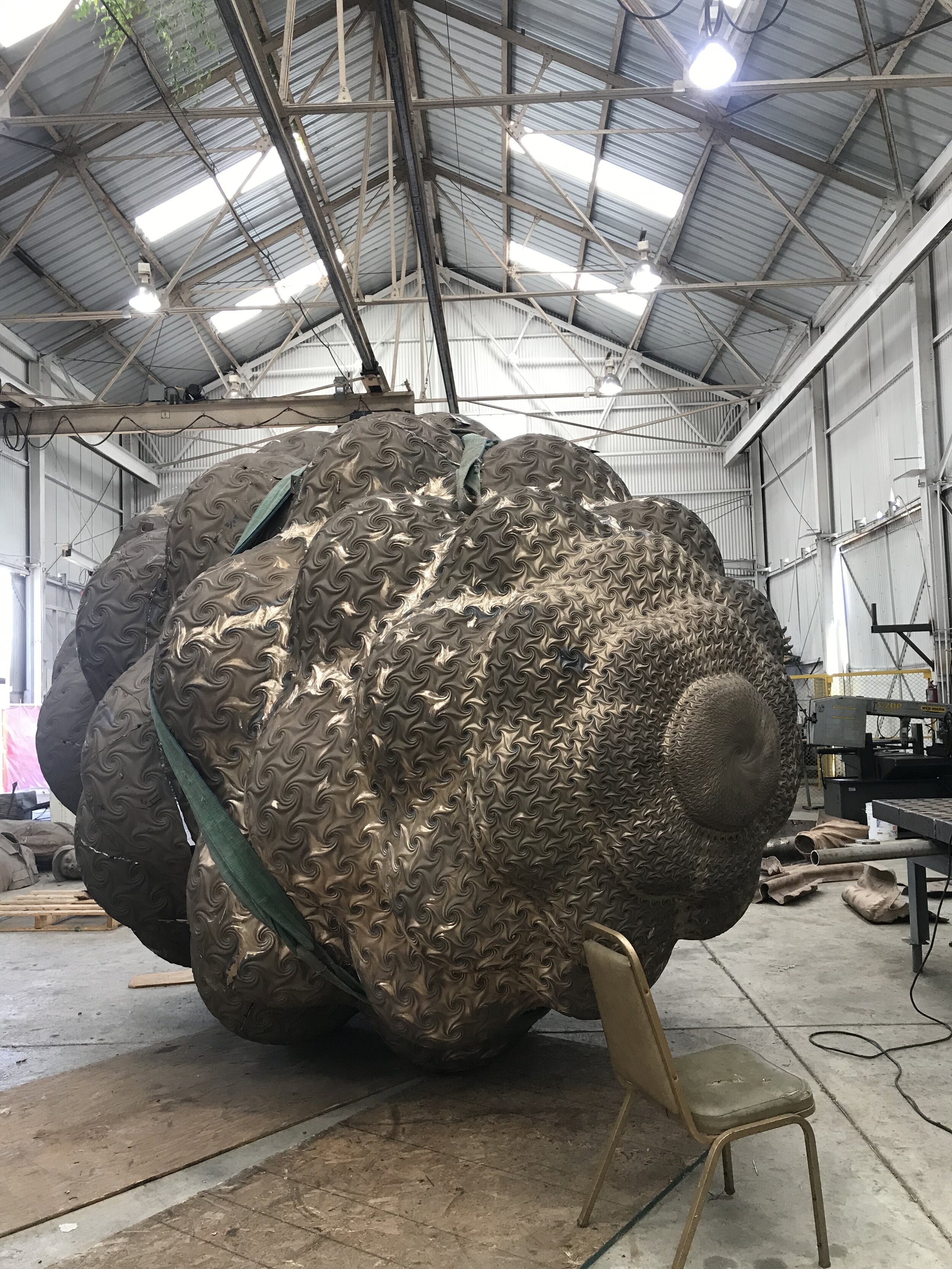
Soft Unveiling
The full form is assembled! The only remaining steps before it is fully complete is giving it a final polish and patina. Here’s Mario and me, pictured at the first public showing of the piece at Artworks Foundry’s Moonlight Pour event.
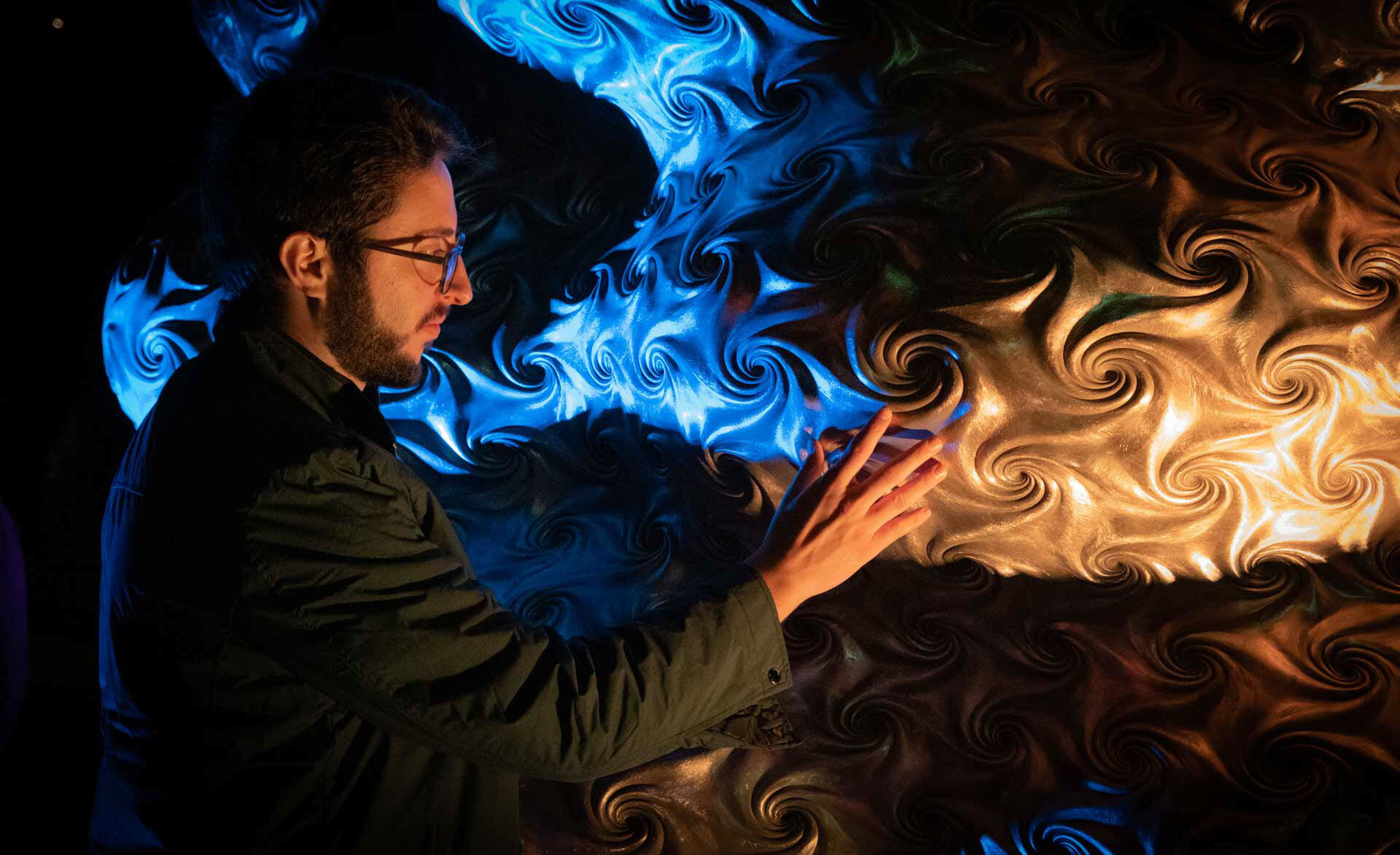